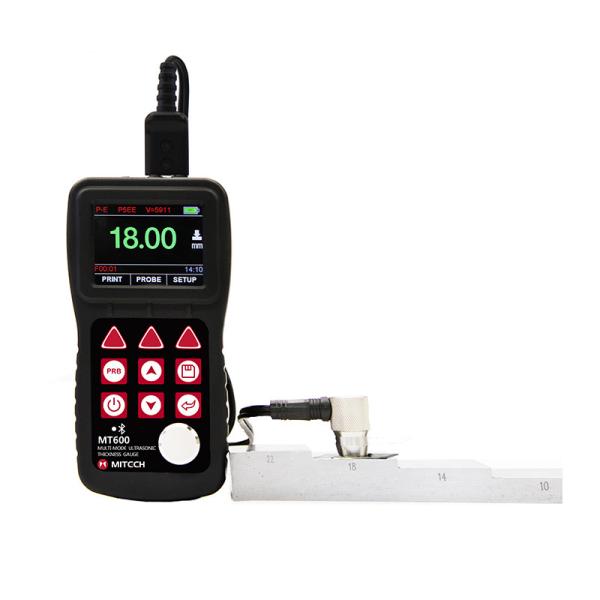
MT600 multi-mode ultrasonic thickness gauge is a upgraded product.
We pay more attention to user experience and innovative features
such as visual experience, protection grade, automatic alarm and
etc..Color TFT display (320×240 TFT LCD) with adjustable backlight,
allow the user to work at worksites with low visibility. IP65
degree of protection, can effectively prevent harsh field
environments of oil, dust and other corrosion. It also has voice
broadcast function, automatic alarm., 0.1mm/0.01mm/0.001mm
resolution, bluetooth communication and penetrate the coating mode
and normal mode functions and etc.. It can measure the substrate
thickness without the need to dispose of coating directly. Its
unique non-destructive testing performance provide the perfect
solution for the thickness testing of closed Pipes, containers,
etc. It is widely used in petroleum, chemical, metallurgy,
shipbuilding, aviation, aerospace and other fields because of
monitoring corrosion thinning degree of various pipes and pressure
vessels.It can also be used for precise measurement of sheet metal
and machined parts. This professional precision instrument is to
improve production efficiency and qualified rate, cost saving.
The digital ultrasonic thickness gauge determines the thickness of
a part or structure by accurately measuring the time required for a
short ultrasonic pulse generated by a transducer to travel through
the thickness of the material, reflect from the back or inside
surface, and be returned to the transducer. The measured two-way
transit time is divided by two to account for the down-and-back
travel path, and then multiplied by the velocity of sound in the
material. The result is expressed in the well-known relationship:
H=v×t/2
Where:
H-Thickness of the test piece.
v-Sound Velocity in the material.
t-The measured round-trip transit time.
Operating Temperature: -20℃~+60℃;
Storage Temperature:-30℃~+70℃
Relative Humidity ≤90%;
The surrounding environment should avoid of vibratin, strong
magentic field, corrosive medium and heavy dust.
Multi-mode: Pulse-Echo mode (P-E mode) and Echo-Echo mode (E-E
mode). In Echo-Echo mode, it can test the wall thickness
eliminating paint or coating thickness.
Wide measuring range:Pulse-Echo mode: (0.65~600)mm (in Steel).
Echo-Echo mode: (2.5~100)mm
V-Path correction to compensate the nonlinearity of the probe
Color TFT display (320×240 TFT LCD) with adjustable backlight,
allow the user to work at worksites with low visibility.
Non-volatile memory can store 100 groups of test thickness. One
hundred records max for each group.
Two AA size alkaline batteries as the power source. Continuous
operating period of no less than 100 hours (default brightness
setting). Display Standby and Auto Power Off functions to save
power.
With internal Bluetooth module, it can print test report
wirelessly.
USB 2.0 communication port. Online transfer of the measured data to
PC via USB
Measuring pipe and tubing.
When measuring a piece of pipe to determine the thickness of the
pipe wall, orientation of the transducers is important. If the
diameter of the pipe is larger than approximately 4 inches,
measurements should be made with the transducer oriented so that
the gap in the wearface is perpendicular (at right angle) to the
long axis of the pipe. For smaller pipe diameters, two measurements
should be performed, one with the wearface gap perpendicular,
another with the gap parallel to the long axis of the pipe. The
smaller of the two displayed values should then be taken as the
thickness at that point.
Measuring hot surfaces
The velocity of sound through a substance is dependant upon its
temperature. As materials heat up, the velocity of sound through
them decreases. In most applications with surface temperatures less
than about 100℃, no special procedures must be observed. At
temperatures above this point, the change in sound velocity of the
material being measured starts to have a noticeable effect upon
ultrasonic measurement. At such elevated temperatures, it is
recommended that the user perform a calibration procedure on a
sample piece of known thickness, which is at or near the
temperature of the material to be measured. This will allow the
gauge to correctly calculate the velocity of sound through the hot
material.
When performing measurements on hot surfaces, it may also be
necessary to use a specially constructed high-temperature
transducer. These transducers are built using materials which can
withstand high temperatures. Even so, it is recommended that the
probe be left in contact with the surface for as short a time as
needed to acquire a stable measurement. While the transducer is in
contact with a hot surface, it will begin to heat up, and through
thermal expansion and other effects, may begin to adversely affect
the accuracy of measurements.
Measuring laminated materials.
Laminated materials are unique in that their density (and therefore
sound-velocity) may vary considerably from one piece to another.
Some laminated materials may even exhibit noticeable changes in
sound-velocity across a single surface. The only way to reliably
measure such materials is by performing a calibration procedure on
a sample piece of known thickness. Ideally, this sample material
should be a part of the same piece being measured, or at least from
the same lamination batch. By calibrating to each test piece
individually, the effects of variation of sound-velocity will be
minimized.
An additional important consideration when measuring laminates, is
that any included air gaps or pockets will cause an early
reflection of the ultrasound beam. This effect will be noticed as a
sudden decrease in thickness in an otherwise regular surface. While
this may impede accurate measurement of total material thickness,
it does provide the user with positive indication of air gaps in
the laminate.
Suitability of materials
Ultrasonic thickness measurements rely on passing a sound wave
through the material being measured. Not all materials are good at
transmitting sound. Ultrasonic thickness measurement is practical
in a wide variety of materials including metals, plastics, and
glass. Materials that are difficult include some cast materials,
concrete, wood, fiberglass, and some rubber.
Couplants
All ultrasonic applications require some medium to couple the sound
from the transducer to the test piece. Typically a high viscosity
liquid is used as the medium. The sound used in ultrasonic
thickness measurement does not travel through air efficiently.
A wide variety of couplant materials may be used in ultrasonic
gauging. Propylene glycol is suitable for most applications. In
difficult applications where maximum transfer of sound energy is
required, glycerin is recommended. However, on some metals glycerin
can promote corrosion by means of water absorption and thus may be
undesirable. Other suitable couplants for measurements at normal
temperatures may include water, various oils and greases, gels, and
silicone fluids. Measurements at elevated temperatures will require
specially formulated high temperature couplants.
Inherent in ultrasonic thickness measurement is the possibility
that the instrument will use the second rather than the first echo
from the back surface of the material being measured while in
standard pulse-echo mode. This may result in a thickness reading
that is TWICE what it should be. The Responsibility for proper use
of the instrument and recognition of these types of phenomenon
rests solely with the user of the instrument.
Mitech CO.,LTD.
Mitech CO.,LTD. located in Beijing, China and was founded in 2004 by a group of doctors and masters graduated from tsinghua or Peking University. It is a professional NDT testing manufacturer, we have our own R&D office for newest and highest technology.
Over ten years, Mitech has always adhered to the business philosophy,
"Technology innovation for development, high quality service as the forward boat", relying on the mastered technology and the tireless pursuit for science and technology, Mitech continuously blends in leading-edge technology to NDT instrument R&D and application, makes the product performance and technical indicators reaching to the international leading level.
From NDT portable instrument to large automatic detection system. Mitech owns intellectual property rights of core technology and it has already applied for invention patents and software copyrights and passed international certification such as EU CE certification and Russian GOST certification etc. Mitech products has been widely used in quality control and safety monitoring of aerospace, petrochemical pipeline, military industry, nuclear industry, ship, automobile, metallurgy, steel structure manufacture, boiler pressure vessel and so on, do the best working for safe operation of industrial production.
Mitech users have spread all over the world such as Japan, Korea, India, Germany, USA etc. By the best quality with competitive price, Mitech had gained a good reputation from global customers. As the professional NDT manufacturer, Mitech will insist our rule of serving for world NDT industry for best and quick development. We are looking for NDT agents from all over the world and welcome knowledgeable people to join us for development.
As professional NDT manufacturer, Mitech will supply you best quality products with competitive price. Professional business team can provide more promotion support according to local market together with our comprehensive experience to help you do professional needs analysis and market protection, launch new products continuously to create more opportunities for long cooperation. Meanwhile, we will support you strong after-sale service to solve more trouble. Any product quality problem within 3 months, we will replace a new one for free, all products with warranty up to two years and life-long maintenance. We will provide maintenance training and accessories with cost price. Mitech has sound market management system to help you manage market precisely and share customer information, establish and standardize market system for long-time win-win cooperation.
Mitech devotes to creating the value for world NDT industry as own duty, unswerving to provide perfect products to the market, providing customers with conscientious service, sincere management to create famous brand.
Mitech is willing to cooperate with world NDT colleagues and makes the efforts for more brilliant tomorrow, struggling for more secure NDT world.